Breakthrough: Mechanical Marvels Walk Without Batteries - Scientists Unveil Groundbreaking 3D-Printed Robots at Fraction of Expected Cost
Science
2025-04-01 03:17:27Content
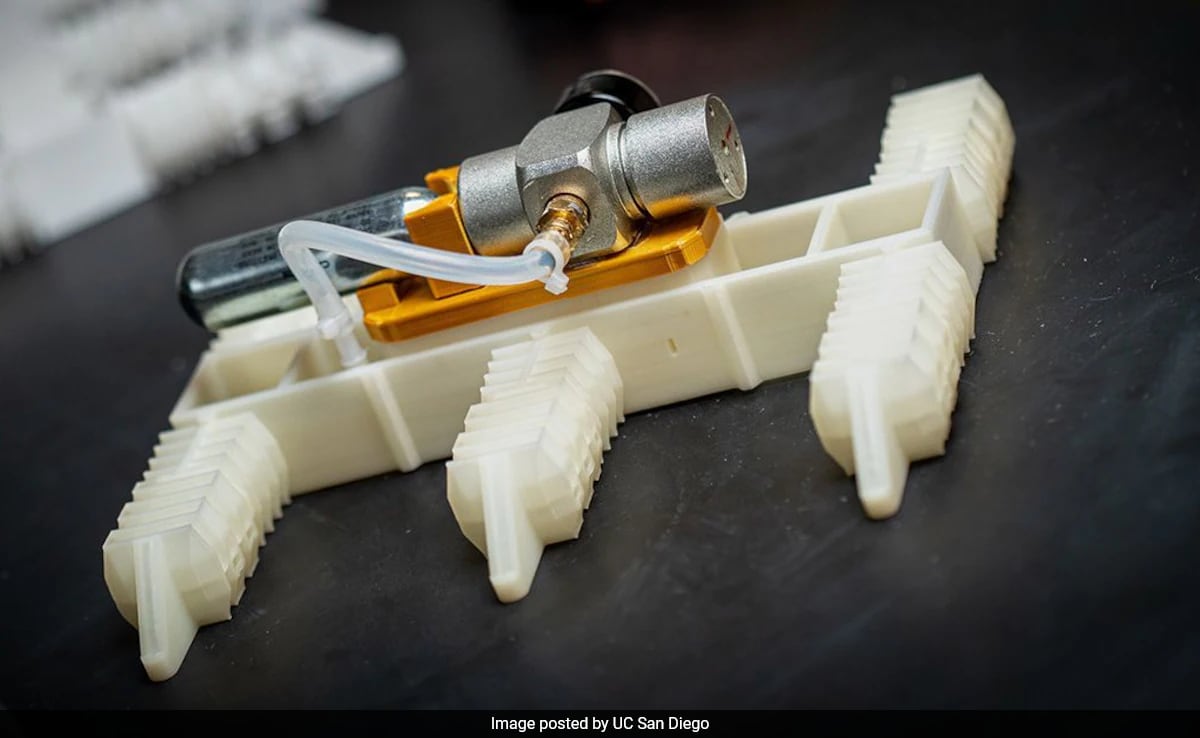
In a groundbreaking leap forward for robotics, scientists have developed an innovative approach to creating robots that challenge traditional manufacturing methods. These cutting-edge machines are designed to emerge directly from 3D printers, featuring a revolutionary design powered by compressed air and constructed from flexible, soft materials.
The research team's vision goes beyond conventional robotic design, focusing on creating machines that are not just functional, but adaptable and seamlessly integrated with their manufacturing process. By utilizing soft, pliable materials and pneumatic power systems, these robots represent a significant advancement in robotic engineering, promising greater versatility and potential applications across multiple fields.
This breakthrough demonstrates how emerging technologies can transform our understanding of robotics, blending advanced manufacturing techniques with intelligent design to create machines that are more responsive, lightweight, and capable of navigating complex environments with unprecedented ease.
Revolutionary Soft Robotics: The Future of Autonomous Printing and Mobility
In the rapidly evolving landscape of technological innovation, researchers are pushing the boundaries of robotics by developing groundbreaking approaches that challenge traditional manufacturing and design paradigms. The intersection of advanced materials science, additive manufacturing, and biomimetic engineering is creating unprecedented opportunities for creating intelligent, adaptable robotic systems that can transform multiple industries.Unleashing the Next Generation of Autonomous Robotic Technologies
Pioneering Flexible Manufacturing Techniques
The emergence of cutting-edge robotic development represents a quantum leap in engineering capabilities. Researchers are now exploring sophisticated methodologies that enable direct fabrication of mobile robotic systems using advanced three-dimensional printing technologies. By integrating pneumatic actuation mechanisms with innovative soft material compositions, scientists are developing robots that can be instantaneously produced and immediately operational. These revolutionary designs transcend traditional rigid robotic architectures, introducing unprecedented flexibility and adaptability. The pneumatic-powered systems leverage compressed air as a primary energy source, enabling complex movement patterns and intricate mechanical behaviors previously unimaginable in conventional robotic platforms.Material Science Breakthroughs in Robotic Design
Contemporary material engineering techniques are fundamental to these transformative robotic innovations. Researchers have developed specialized polymeric compounds that exhibit remarkable mechanical properties, including exceptional elasticity, durability, and responsiveness. These advanced materials allow for the creation of robots that can dynamically adjust their structural configuration in response to environmental stimuli. The integration of soft, flexible materials represents a paradigm shift in robotic design philosophy. Unlike traditional metallic or rigid constructions, these new robotic systems can seamlessly navigate complex terrains, compress, expand, and adapt with unprecedented efficiency. The potential applications span multiple domains, from medical interventions to exploration of challenging geographical landscapes.Pneumatic Actuation: A Game-Changing Mobility Mechanism
Compressed air emerges as a revolutionary propulsion mechanism in these next-generation robotic systems. By strategically manipulating air pressure within intricate internal channels, researchers can generate complex locomotion patterns that mimic biological movement principles. This approach eliminates traditional mechanical limitations associated with electric motors and mechanical actuators. The pneumatic actuation methodology enables robots to perform nuanced movements with minimal energy expenditure. Complex locomotion strategies can be programmed directly into the material's structural design, creating self-configuring systems that can traverse diverse environmental conditions with remarkable precision and efficiency.Implications for Future Technological Ecosystems
The convergence of advanced manufacturing techniques, material science, and robotic engineering heralds a new era of technological possibilities. These soft, air-powered robotic systems represent more than mere technological curiosities; they embody a fundamental reimagining of how autonomous machines can interact with their environment. Potential applications extend across numerous critical domains, including medical robotics, environmental monitoring, search and rescue operations, and advanced manufacturing processes. The ability to produce fully functional robotic systems directly from a three-dimensional printing platform represents a revolutionary approach to technological development and deployment.Challenges and Future Research Directions
Despite remarkable progress, significant research challenges remain. Scientists must continue refining material compositions, improving pneumatic control mechanisms, and developing more sophisticated computational models to predict and optimize robotic behavior. Interdisciplinary collaboration will be crucial in translating these promising laboratory prototypes into practical, real-world applications. The ongoing evolution of soft robotics promises to redefine our understanding of autonomous systems, blurring the boundaries between biological and mechanical intelligence. As researchers continue to push technological boundaries, we stand on the cusp of a transformative era in robotic innovation.RELATED NEWS
Science
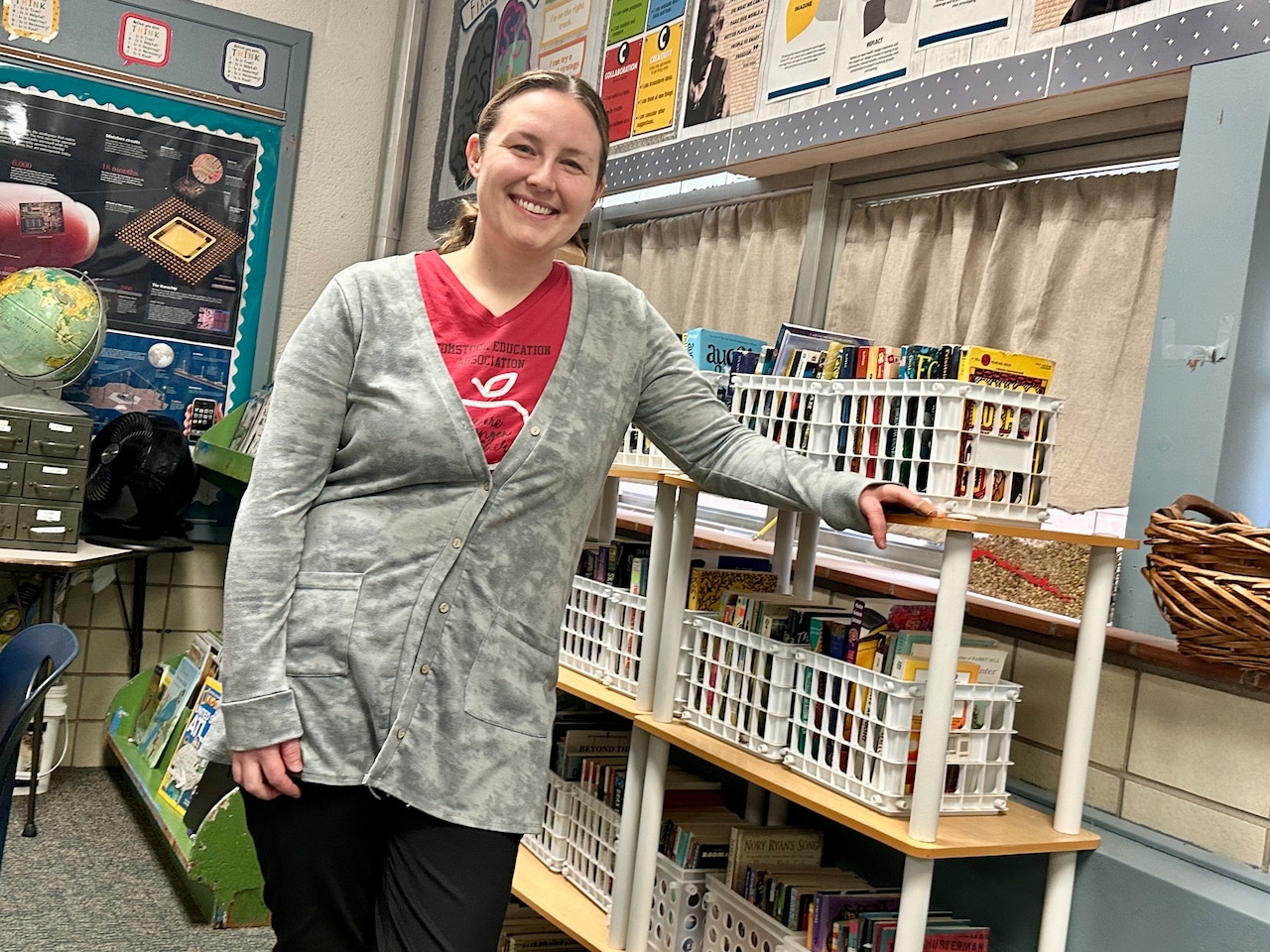
Chaos in the Classroom: How Michigan's Top Science Educator Turns Disorder into Discovery
2025-03-03 12:10:00
Science
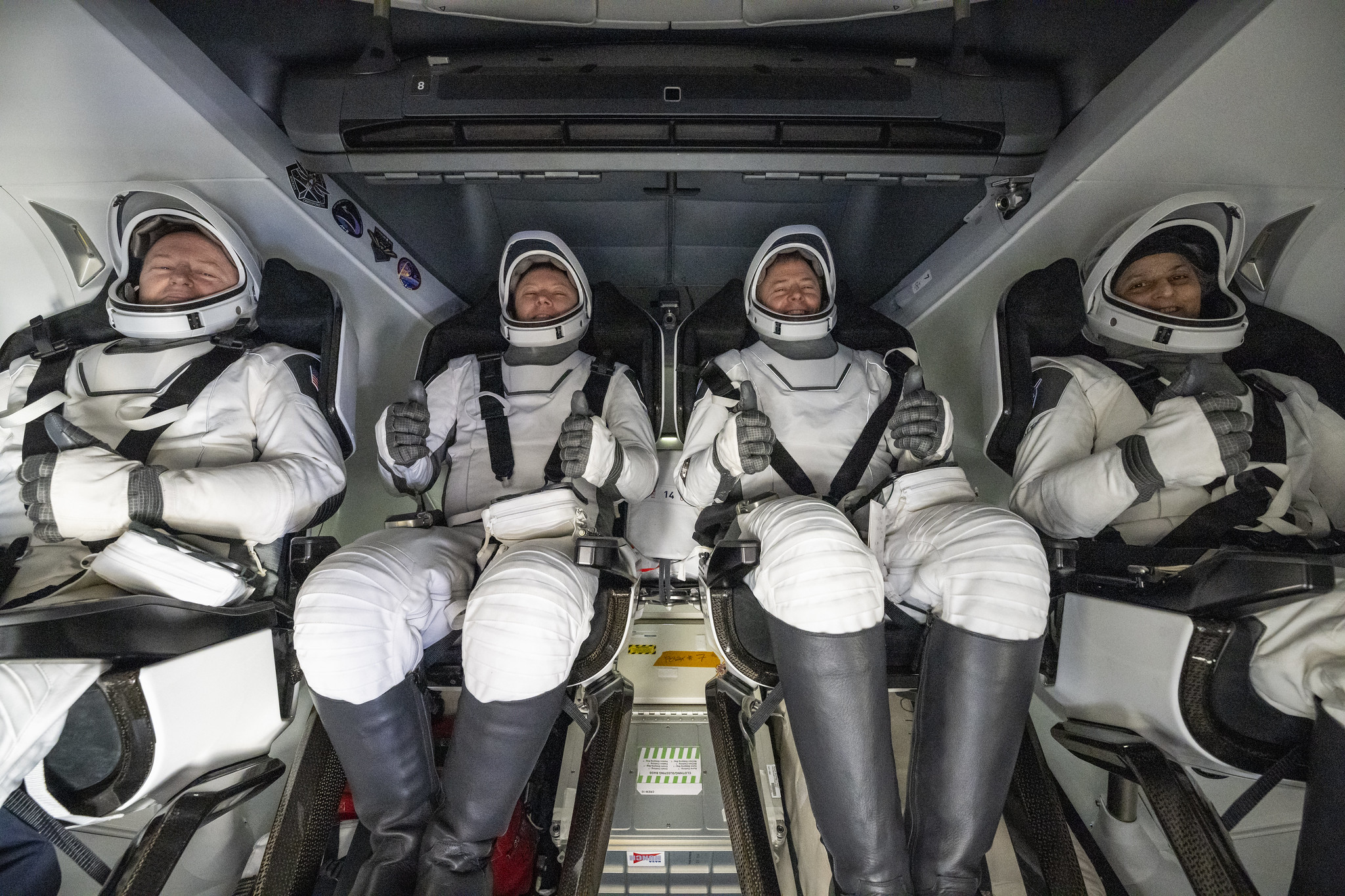
Space Explorers Reveal Secrets: Inside NASA and SpaceX's Latest Cosmic Expedition
2025-03-24 14:03:02