Driving the Future: How Ericsson Supercharges Jaguar Land Rover's Tech Revolution
Manufacturing
2025-02-18 14:11:50Content
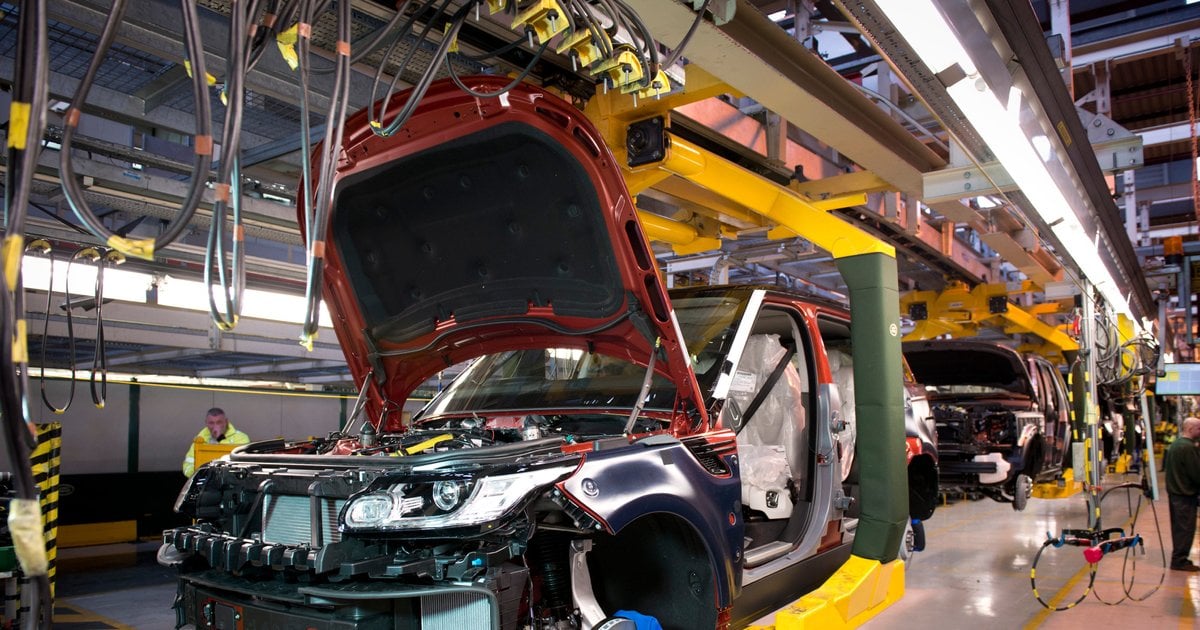
In a groundbreaking digital transformation, Jaguar Land Rover (JLR) is revolutionizing its vehicle manufacturing process by fully embracing Industry 4.0 technologies. At the heart of this technological leap is Ericsson's cutting-edge Private 5G network, which is helping the automotive manufacturer dramatically streamline its operations and eliminate traditional wired infrastructure.
The innovative "cut the copper" approach represents a significant milestone in JLR's digital manufacturing strategy. By leveraging Ericsson's Private 5G solution, the company is creating a more flexible, efficient, and responsive production environment. This wireless technology enables real-time communication, enhanced automation, and unprecedented connectivity across the manufacturing floor.
Gone are the days of complex, rigid copper wire networks. Ericsson's Private 5G provides JLR with a robust, secure, and ultra-low latency wireless network that supports advanced technologies like Internet of Things (IoT) devices, autonomous robots, and smart manufacturing systems. The result is a more agile, intelligent manufacturing ecosystem that can quickly adapt to changing production demands.
By cutting the copper and embracing wireless connectivity, JLR is not just upgrading its infrastructure—it's reimagining the future of automotive manufacturing. This bold move positions the company at the forefront of the Industry 4.0 revolution, demonstrating how advanced telecommunications can transform traditional industrial processes.
Digital Revolution: How Private 5G Networks Are Transforming Automotive Manufacturing
In the rapidly evolving landscape of industrial technology, automotive manufacturers are pioneering groundbreaking strategies to revolutionize production processes. The convergence of advanced telecommunications and manufacturing represents a pivotal moment in industrial innovation, where cutting-edge connectivity solutions are redefining operational efficiency and technological capabilities.Unleashing the Power of Next-Generation Manufacturing Connectivity
The Technological Paradigm Shift in Automotive Production
The automotive manufacturing sector stands at a critical juncture of technological transformation. Traditional manufacturing infrastructures are being systematically dismantled and reconstructed through sophisticated digital ecosystems. Private 5G networks emerge as a transformative technology, offering unprecedented levels of connectivity, reliability, and operational flexibility. Manufacturers like Jaguar Land Rover are strategically implementing these advanced network infrastructures to fundamentally reimagine their production environments. By leveraging private 5G technologies, they are creating intelligent, responsive manufacturing spaces that can adapt in real-time to complex operational demands.Wireless Connectivity: Eliminating Infrastructure Limitations
The traditional reliance on copper-based communication infrastructures represents a significant technological bottleneck. Private 5G networks provide a revolutionary alternative, enabling manufacturers to dramatically reduce physical infrastructure dependencies while simultaneously enhancing network performance and reliability. These wireless networks offer remarkable advantages, including ultra-low latency, high bandwidth, and robust security protocols. By eliminating extensive copper cabling, manufacturers can create more flexible, adaptable production environments that can be rapidly reconfigured to meet changing market demands.Industry 4.0: The Technological Convergence
Industry 4.0 represents a comprehensive digital transformation strategy that integrates advanced technologies like artificial intelligence, Internet of Things (IoT), and sophisticated networking solutions. Private 5G networks serve as a critical infrastructure component, enabling seamless communication between complex manufacturing systems. The integration of these technologies creates intelligent manufacturing ecosystems where machines, sensors, and production systems communicate instantaneously, optimizing processes, reducing downtime, and enhancing overall operational efficiency. This technological convergence represents a fundamental reimagining of industrial production methodologies.Technical Architecture and Implementation Strategies
Implementing private 5G networks requires sophisticated technical planning and strategic infrastructure development. Manufacturers must carefully design network architectures that can support high-density device connections, ensure robust security protocols, and provide consistent, low-latency performance across complex manufacturing environments. Key implementation considerations include spectrum allocation, edge computing integration, cybersecurity frameworks, and comprehensive network management systems. These technical considerations demand a holistic approach that balances technological capabilities with practical operational requirements.Economic and Operational Implications
The adoption of private 5G networks represents a significant economic investment with potentially transformative returns. By reducing infrastructure costs, enhancing operational efficiency, and creating more adaptable manufacturing environments, companies can achieve substantial competitive advantages. Manufacturers can expect improved production metrics, reduced maintenance costs, enhanced quality control processes, and increased overall operational agility. The long-term economic benefits of these technological investments extend far beyond immediate infrastructure improvements.Future Technological Trajectories
As private 5G technologies continue to evolve, their potential applications in manufacturing will expand exponentially. Future iterations may incorporate advanced artificial intelligence, more sophisticated machine learning algorithms, and increasingly complex autonomous systems. The ongoing technological convergence suggests that private 5G networks will become fundamental infrastructure components across multiple industrial sectors, not just automotive manufacturing. This represents a broader technological revolution with far-reaching implications for global industrial production.RELATED NEWS
Manufacturing
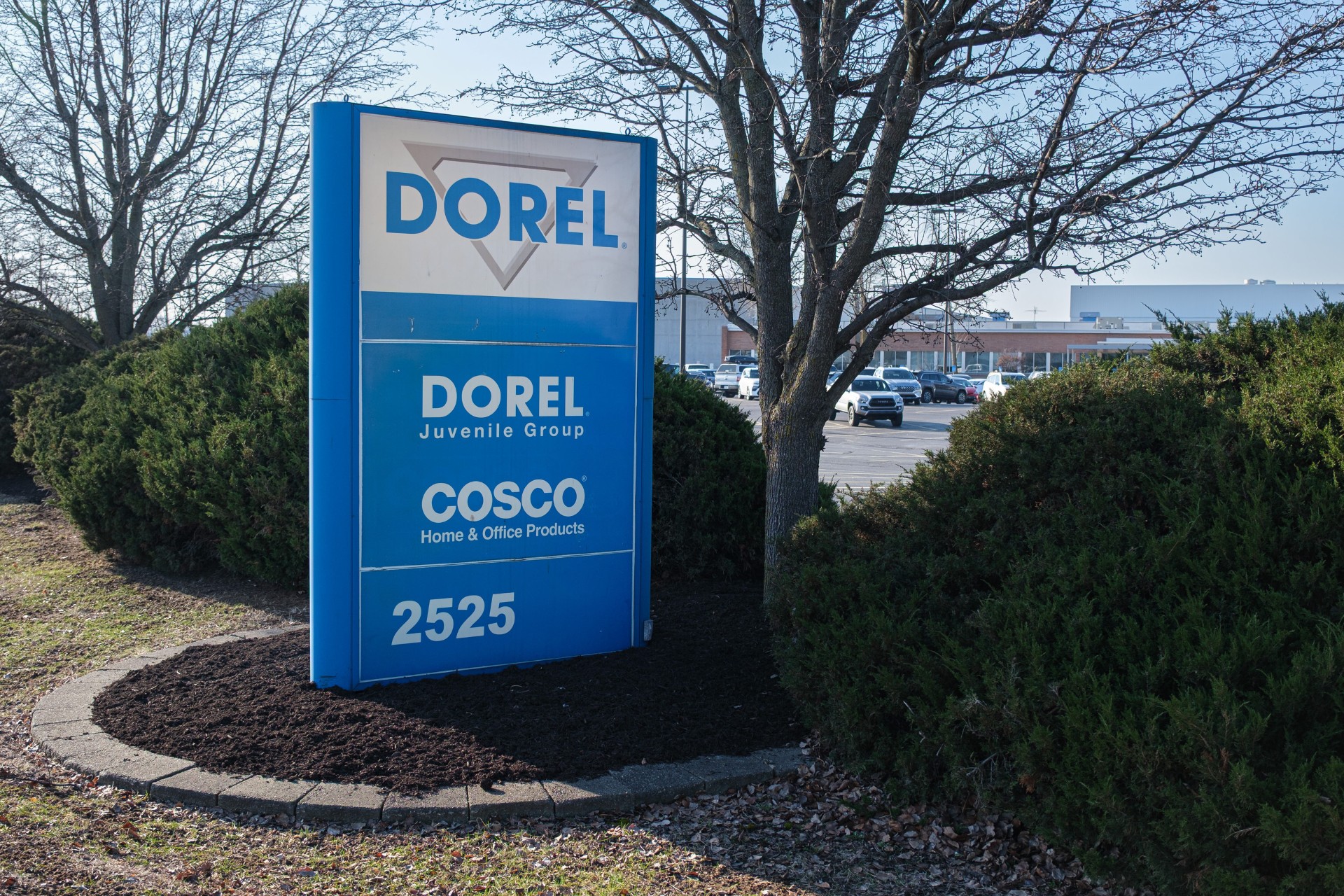
Strategic Shift: Dorel Industries Unloads Columbus Facility in Savvy Real Estate Move
2025-03-11 15:00:01
Manufacturing
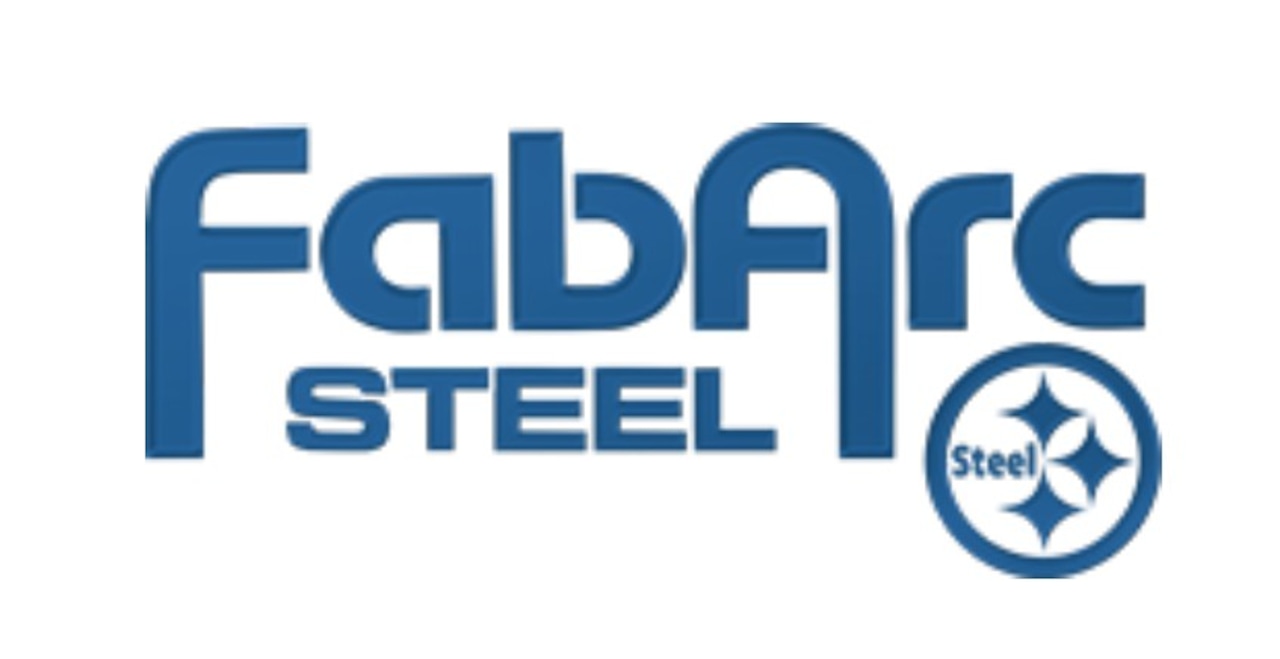
Driving Growth: Alabama Steel Titan Lands Massive $100M Auto Manufacturing Deal
2025-03-06 14:31:25
Manufacturing
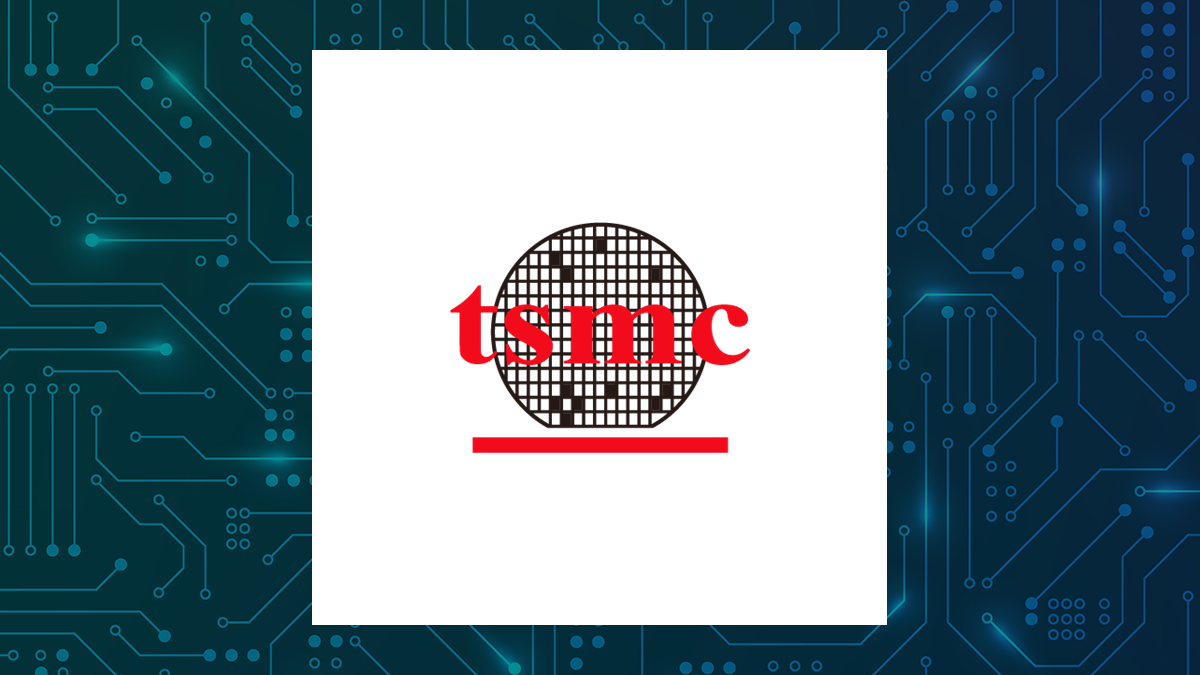
Chip Investment Surge: Hong Kong Asset Manager Boosts Stake in Taiwan Semiconductor Giant
2025-02-23 11:00:53