Bridging the Skills Gap: How Ohio's Tech Schools Are Rescuing Manufacturing's Future
Manufacturing
2025-02-20 23:47:00Content
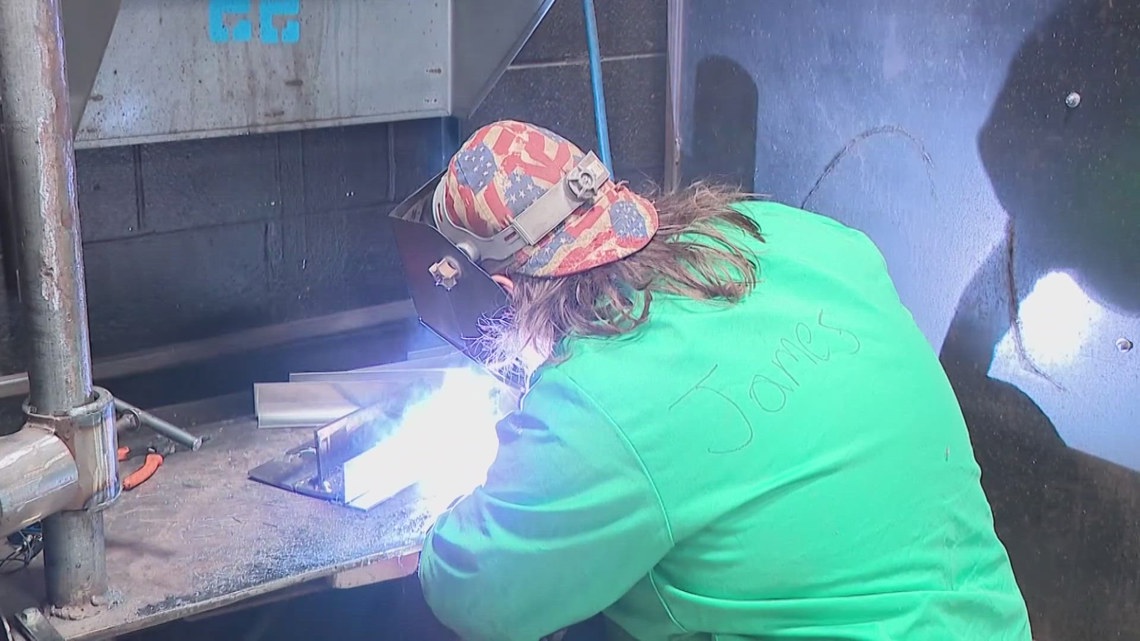
In today's rapidly evolving industrial landscape, manufacturers are facing a critical shortage of skilled trades professionals. The demand for specialized workers has reached a fever pitch, with companies urgently seeking talented individuals to fill crucial roles that keep the wheels of industry turning.
Welders, machinists, robotics engineers, carpenters, and electricians are now more valuable than ever. These skilled craftspeople are the backbone of modern manufacturing, bridging the gap between cutting-edge technology and practical production. From precision metalwork to advanced robotic systems, these professionals are in extraordinarily high demand, with employers competing fiercely to attract and retain top talent.
The skills gap has become a pressing challenge for industries across the board. As traditional manufacturing transforms and technology continues to advance, the need for highly trained, adaptable workers has never been more acute. Companies are increasingly recognizing that their success depends on finding and nurturing these specialized professionals who can navigate the complex intersection of technical expertise and hands-on craftsmanship.
The Skilled Labor Crisis: America's Industrial Workforce Transformation
In the rapidly evolving landscape of modern manufacturing, a critical challenge emerges that threatens the very foundation of industrial productivity. The United States stands at a pivotal crossroads, where technological advancement and workforce development intersect, creating an unprecedented demand for specialized technical professionals who can bridge the gap between traditional craftsmanship and cutting-edge technological innovation.Bridging the Skills Gap: A National Economic Imperative
The Changing Face of Industrial Employment
The contemporary manufacturing sector is experiencing a profound metamorphosis, driven by technological disruption and complex economic dynamics. Traditional vocational roles are no longer simple manual labor positions but have transformed into sophisticated technical careers requiring advanced skills, technological literacy, and adaptive problem-solving capabilities. Manufacturers across the nation are confronting an increasingly complex recruitment landscape, where finding qualified professionals has become a strategic challenge that extends far beyond conventional hiring practices. Robotics integration, advanced manufacturing technologies, and sophisticated automation systems demand a new breed of technical professionals who can seamlessly navigate complex technological ecosystems. These professionals must possess not just technical expertise, but also the intellectual flexibility to continuously learn and adapt to rapidly changing industrial environments.Critical Skill Domains in High Demand
The current industrial ecosystem reveals several critical skill domains experiencing unprecedented demand. Welding, once considered a straightforward trade, now requires advanced certifications and understanding of complex metallurgical principles. Modern welders must comprehend advanced materials science, precision engineering techniques, and sophisticated equipment operation. Machinists represent another crucial professional category experiencing significant transformation. Contemporary machining demands intricate knowledge of computer-aided design, precision manufacturing technologies, and advanced computational skills. These professionals are no longer simply operating machinery but are integral engineers who design, program, and optimize complex manufacturing processes.Technological Convergence and Workforce Development
The intersection of technological innovation and workforce development represents a complex challenge requiring multi-stakeholder collaboration. Educational institutions, industry leaders, government agencies, and technical training programs must develop comprehensive strategies to address the growing skills gap. Robotics engineering emerges as a particularly critical domain, representing the cutting edge of industrial technological evolution. These professionals design, develop, and implement sophisticated automated systems that drive efficiency, productivity, and technological innovation across multiple industrial sectors.Economic and Social Implications
The skilled labor shortage extends beyond mere recruitment challenges, representing a significant economic and social transformation. As manufacturing becomes increasingly technology-driven, the workforce must rapidly adapt to maintain global competitiveness. This transition requires substantial investments in education, training infrastructure, and innovative workforce development strategies. Electricians and carpenters, traditionally viewed as fundamental trade professionals, now require advanced technological understanding. Modern electrical systems integrate complex digital technologies, while contemporary carpentry involves sophisticated design technologies, sustainable materials science, and advanced computational planning tools.Strategic Workforce Transformation
Addressing the skilled labor crisis demands a holistic, forward-thinking approach. Comprehensive strategies must include enhanced vocational training programs, industry-academic partnerships, targeted recruitment initiatives, and continuous professional development opportunities. Employers must reimagine recruitment, offering competitive compensation packages, robust training programs, and clear career progression pathways. By positioning technical careers as dynamic, intellectually stimulating professional opportunities, industries can attract and retain the next generation of skilled professionals.RELATED NEWS
Manufacturing
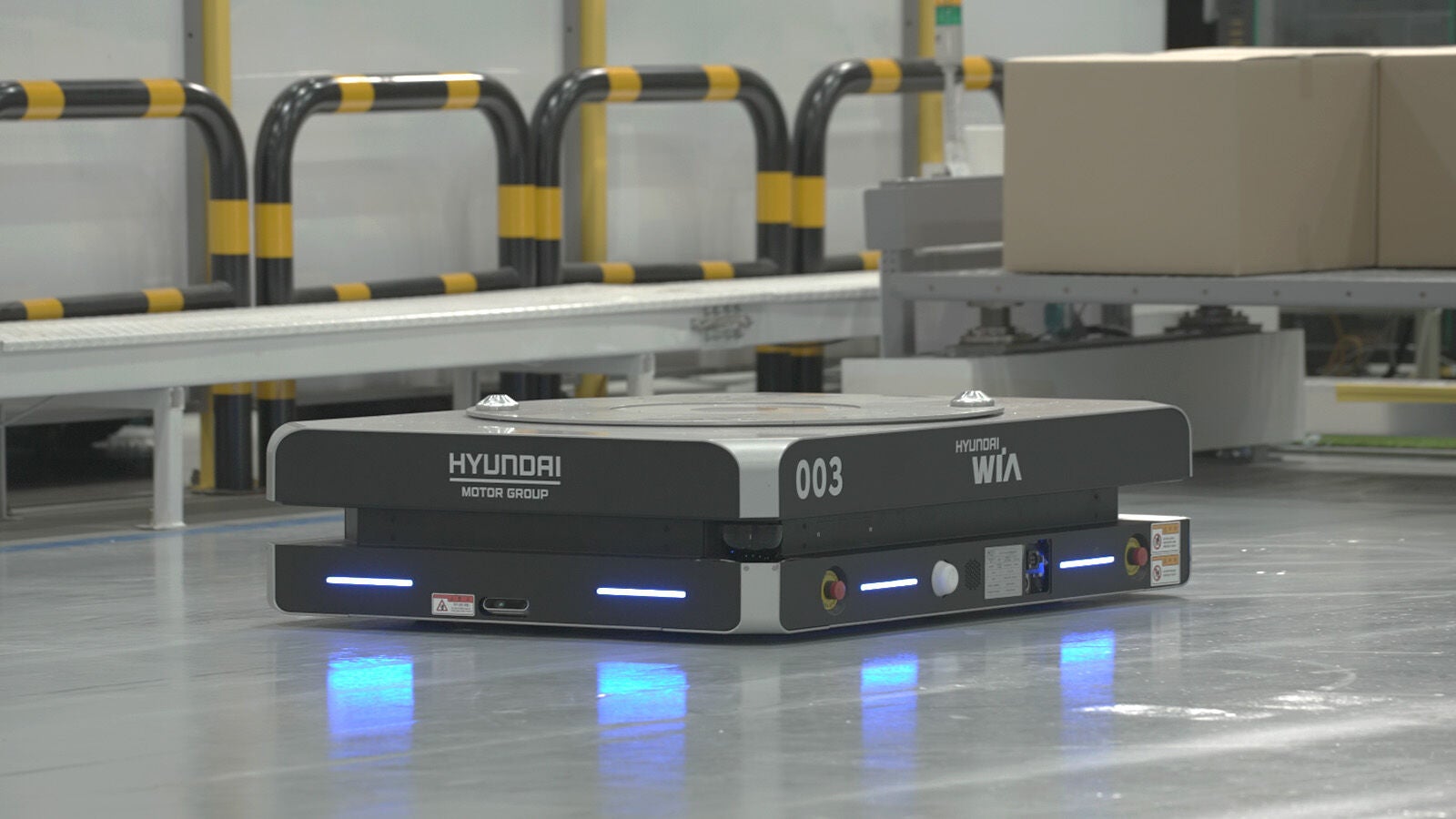
Korean Tech Giants Revolutionize Smart Manufacturing with Next-Gen 5G Innovation
2025-02-27 09:06:27
Manufacturing
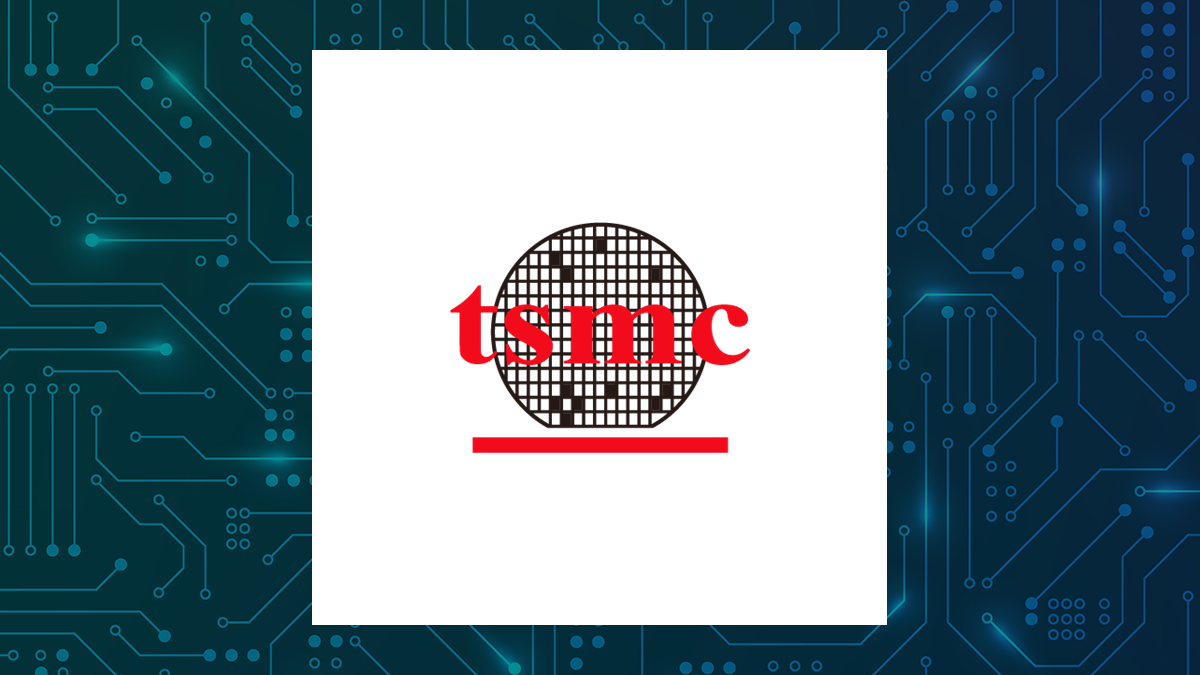
Investor Shift: M. Kulyk & Associates Trims Stakes in Tech Giant Taiwan Semiconductor
2025-03-09 11:38:16