Breaking: AI Breakthrough Unlocks Titanium's Hidden Potential in Record-Speed Manufacturing
Manufacturing
2025-03-07 16:18:52Content
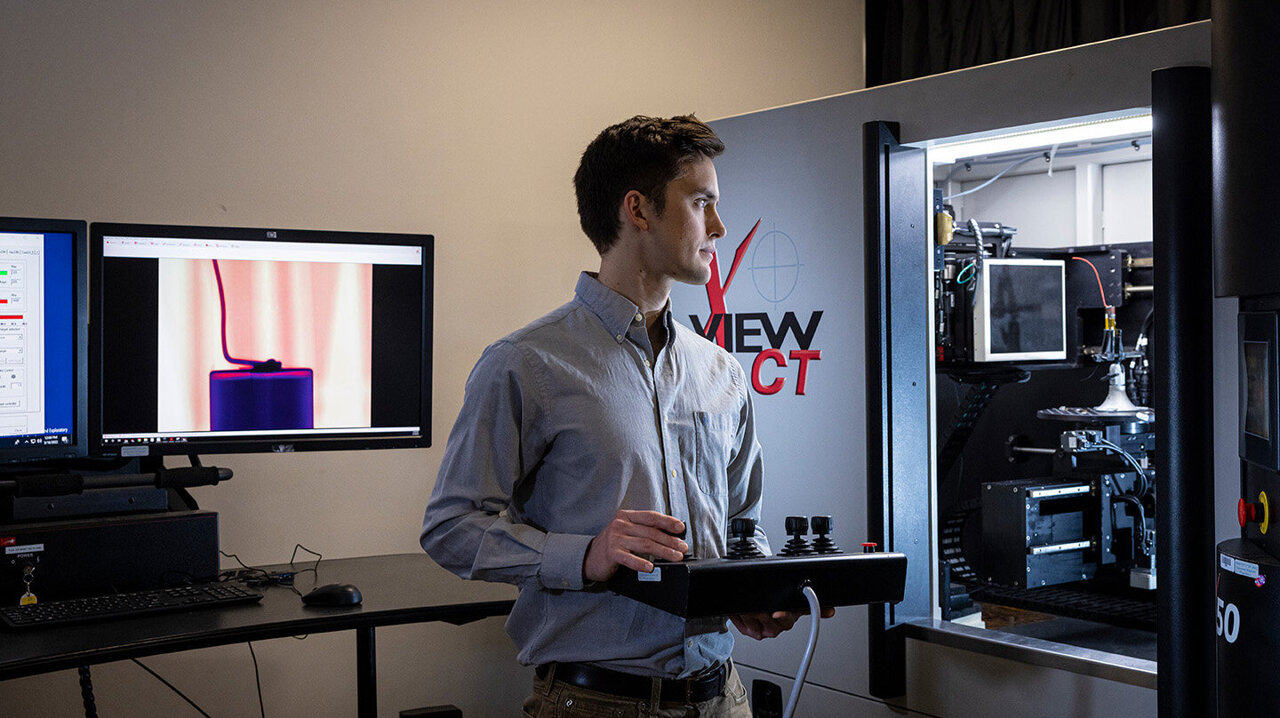
Revolutionizing Manufacturing: A Breakthrough in Titanium Alloy Production
The world of advanced manufacturing has long grappled with a challenging bottleneck: creating high-performance titanium alloy components. From cutting-edge spacecraft and sophisticated submarines to life-changing medical devices, the traditional production methods have been notoriously slow and resource-consuming. Even with the advent of advanced metal 3D-printing technologies, manufacturers have struggled to streamline the process of crafting these critical, precision-engineered parts.
Titanium alloys represent a pinnacle of engineering materials—lightweight, incredibly strong, and resistant to extreme conditions. However, their complex production has historically demanded significant time, energy, and financial investment. Engineers and materials scientists have been searching for a more efficient approach that could dramatically reduce production constraints while maintaining the exceptional quality required for mission-critical applications.
The current landscape of manufacturing these specialized components involves intricate processes that test the limits of technological innovation. Researchers and industry experts continue to push boundaries, seeking breakthrough methods that can transform how we create these essential high-performance materials.
Revolutionary Breakthrough: Transforming Titanium Alloy Manufacturing with Cutting-Edge Technology
In the ever-evolving landscape of advanced manufacturing, a groundbreaking innovation is poised to revolutionize the production of high-performance titanium alloy components. This transformative approach promises to address long-standing challenges in creating critical parts for aerospace, marine, and medical industries, potentially reshaping how we approach material engineering and precision manufacturing.Unlocking the Future of Advanced Material Production: A Technological Quantum Leap
The Complex Landscape of Titanium Alloy Manufacturing
Titanium alloy production has historically been a labyrinthine process fraught with significant technological and economic challenges. Traditional manufacturing methods have been constrained by extensive time investments, substantial resource consumption, and intricate technical limitations. Engineers and materials scientists have long sought a breakthrough that could fundamentally reimagine the approach to creating these critical components. The complexity of titanium alloy fabrication stems from its unique metallurgical properties. Unlike more malleable metals, titanium requires extraordinary precision and sophisticated technological interventions to manipulate its molecular structure effectively. Manufacturers have been compelled to navigate a delicate balance between maintaining material integrity and achieving desired structural characteristics.Technological Innovations Driving Transformation
Recent advancements in additive manufacturing and computational materials science have opened unprecedented pathways for reimagining titanium alloy production. Cutting-edge 3D printing technologies now enable unprecedented levels of precision and efficiency, dramatically reducing the traditional barriers that have historically impeded rapid component development. Sophisticated algorithms and machine learning models are now being deployed to optimize material composition and printing parameters. These intelligent systems can predict and mitigate potential structural weaknesses, ensuring that each manufactured component meets exacting performance standards. By integrating real-time monitoring and adaptive manufacturing techniques, researchers are creating a new paradigm of material production.Interdisciplinary Implications and Potential Applications
The ramifications of this technological breakthrough extend far beyond traditional manufacturing domains. Aerospace engineers can now contemplate lighter, more resilient spacecraft components. Medical device manufacturers might develop more intricate and personalized implants with enhanced biocompatibility. Submarine and naval engineering could benefit from components with superior corrosion resistance and structural integrity. Quantum computational techniques are being leveraged to simulate molecular interactions at unprecedented scales, allowing researchers to understand and manipulate titanium alloy characteristics with remarkable granularity. This approach represents a fundamental shift from empirical trial-and-error methodologies to a more predictive, data-driven manufacturing paradigm.Economic and Environmental Considerations
Beyond technical achievements, this innovation carries profound economic and environmental implications. By dramatically reducing resource consumption and manufacturing time, the new approach could significantly lower production costs. Moreover, the enhanced efficiency translates to reduced energy expenditure and minimized material waste, aligning with global sustainability objectives. The potential cost reductions could democratize access to high-performance materials, enabling smaller organizations and research institutions to engage in advanced manufacturing processes that were previously prohibitively expensive. This technological democratization could accelerate innovation across multiple industrial sectors.Future Research and Development Trajectories
As researchers continue to refine these groundbreaking methodologies, the horizon of possibilities continues to expand. Collaborative efforts between materials scientists, computational experts, and industry practitioners are creating a dynamic ecosystem of continuous innovation. Emerging research suggests that these techniques might be adaptable to other complex alloy systems, potentially triggering a comprehensive transformation in how we conceptualize and execute advanced material production. The interdisciplinary nature of this work underscores the increasingly collaborative and integrated approach required to solve complex technological challenges.RELATED NEWS
Manufacturing
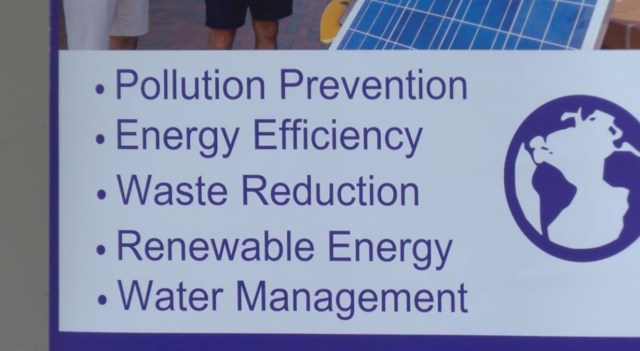
Bridging Industry Gaps: ECU's Manufacturing Summit Unites Local Business Leaders
2025-02-27 19:08:30
Manufacturing
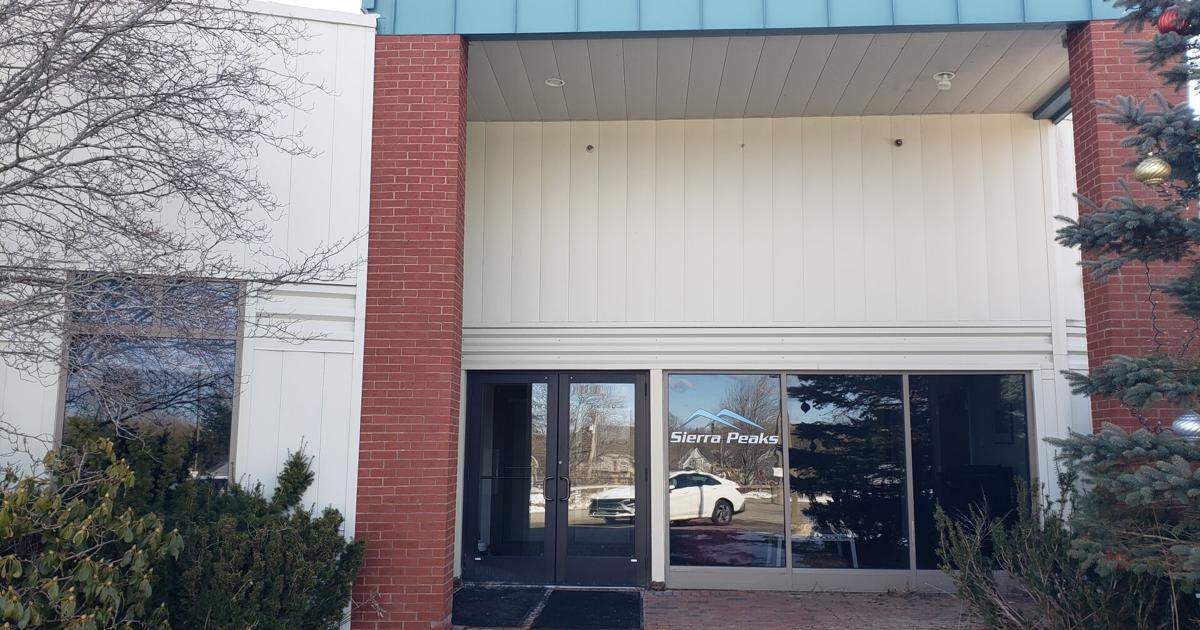
Shock Waves in Rockland: Local Manufacturing Giant Shutters Operations
2025-03-08 17:59:00
Manufacturing
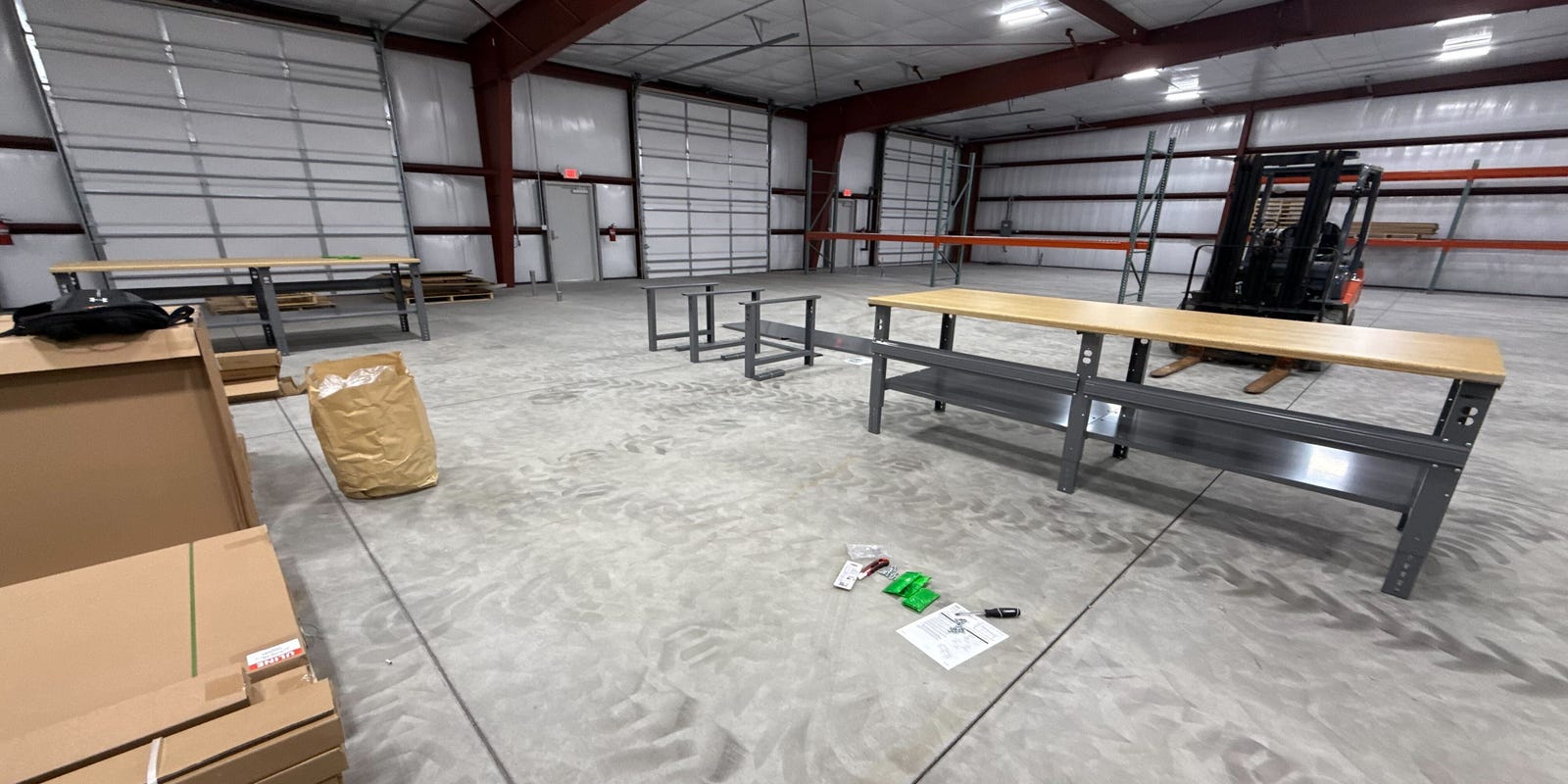
High-Tech Haven: Unveiling Wilmington's Cutting-Edge Computer Manufacturing Hub
2025-02-26 10:06:32