Metal Revolution: How Small Manufacturers Are Transforming 3D Printing
Manufacturing
2025-02-14 18:10:00Content

The landscape of manufacturing is undergoing a transformative revolution, with additive manufacturing (AM) metal-laser-welding technologies emerging as a game-changing solution for small and medium-sized enterprises. These cutting-edge processes are offering a sustainable and economically attractive alternative to traditional machining and milling techniques.
Rapid advancements in hardware, sophisticated software, and integrative robotic technologies are propelling 3D metal printing from a niche technology into mainstream manufacturing. This evolution brings unprecedented advantages of speed, precision, and adaptability directly to smaller manufacturers who previously faced significant technological barriers.
Original equipment manufacturers (OEMs) and technology integrators are now actively developing specialized metal 3D-printing systems specifically designed to address the unique challenges faced by small and medium-sized businesses. By democratizing access to advanced manufacturing technologies, these innovations are empowering companies to enhance their production capabilities, reduce costs, and compete more effectively in a rapidly changing global marketplace.
Revolutionary Metal 3D Printing: Transforming Manufacturing for Small and Medium Enterprises
In the rapidly evolving landscape of industrial innovation, a technological revolution is quietly reshaping the manufacturing sector. Small and medium-sized enterprises are witnessing a transformative moment as cutting-edge additive manufacturing technologies emerge, promising to redefine traditional production methodologies and unlock unprecedented potential for innovation and efficiency.Breakthrough Technologies Reshaping Industrial Production
The Emergence of Advanced Additive Manufacturing
The manufacturing world stands on the precipice of a technological metamorphosis driven by sophisticated metal 3D printing technologies. Unlike conventional machining techniques, these advanced systems represent a quantum leap in production capabilities. Original equipment manufacturers (OEMs) are investing heavily in developing intricate robotic systems that can translate complex digital designs into precise metal components with remarkable accuracy. Modern metal 3D printing technologies leverage sophisticated laser welding processes that enable unprecedented levels of precision and complexity. Engineers and designers can now create intricate geometries that were previously impossible or prohibitively expensive using traditional manufacturing methods. The integration of advanced software algorithms with high-precision robotic systems allows for unprecedented design flexibility and manufacturing efficiency.Technological Convergence in Manufacturing Innovation
The convergence of hardware, software, and robotic technologies is creating a new paradigm in industrial production. Sophisticated machine learning algorithms now enable 3D printing systems to optimize manufacturing processes in real-time, reducing material waste and improving overall production efficiency. These intelligent systems can analyze complex design parameters, predict potential manufacturing challenges, and automatically adjust printing strategies to ensure optimal output. Small and medium-sized enterprises are particularly well-positioned to benefit from these technological advancements. The reduced capital investment required for advanced 3D metal printing systems compared to traditional manufacturing equipment makes these technologies increasingly accessible. Companies can now prototype and produce complex metal components with significantly lower upfront costs and faster turnaround times.Economic and Sustainability Implications
Beyond technological capabilities, metal 3D printing represents a significant stride towards sustainable manufacturing practices. The additive manufacturing process inherently reduces material waste compared to subtractive manufacturing techniques. By building components layer by layer, these technologies minimize raw material consumption and energy expenditure. Furthermore, the ability to produce complex, lightweight components with intricate internal structures opens new possibilities across multiple industries. Aerospace, automotive, medical device manufacturing, and precision engineering sectors are experiencing radical transformations as these technologies mature. The potential for creating highly customized, performance-optimized components is revolutionizing product design and engineering approaches.Future Trajectory of Additive Manufacturing
As research and development continue to push technological boundaries, metal 3D printing is expected to become increasingly sophisticated. Emerging technologies are exploring multi-material printing capabilities, enhanced resolution, and faster production speeds. The integration of artificial intelligence and advanced materials science promises to unlock even more remarkable manufacturing capabilities in the coming years. Researchers and industrial engineers are continuously developing more advanced laser welding techniques, exploring novel metal alloys, and creating more intelligent robotic systems. The future of manufacturing will likely see a seamless integration of digital design, advanced materials, and intelligent robotic systems that can produce increasingly complex and customized components with unprecedented efficiency.RELATED NEWS
Manufacturing
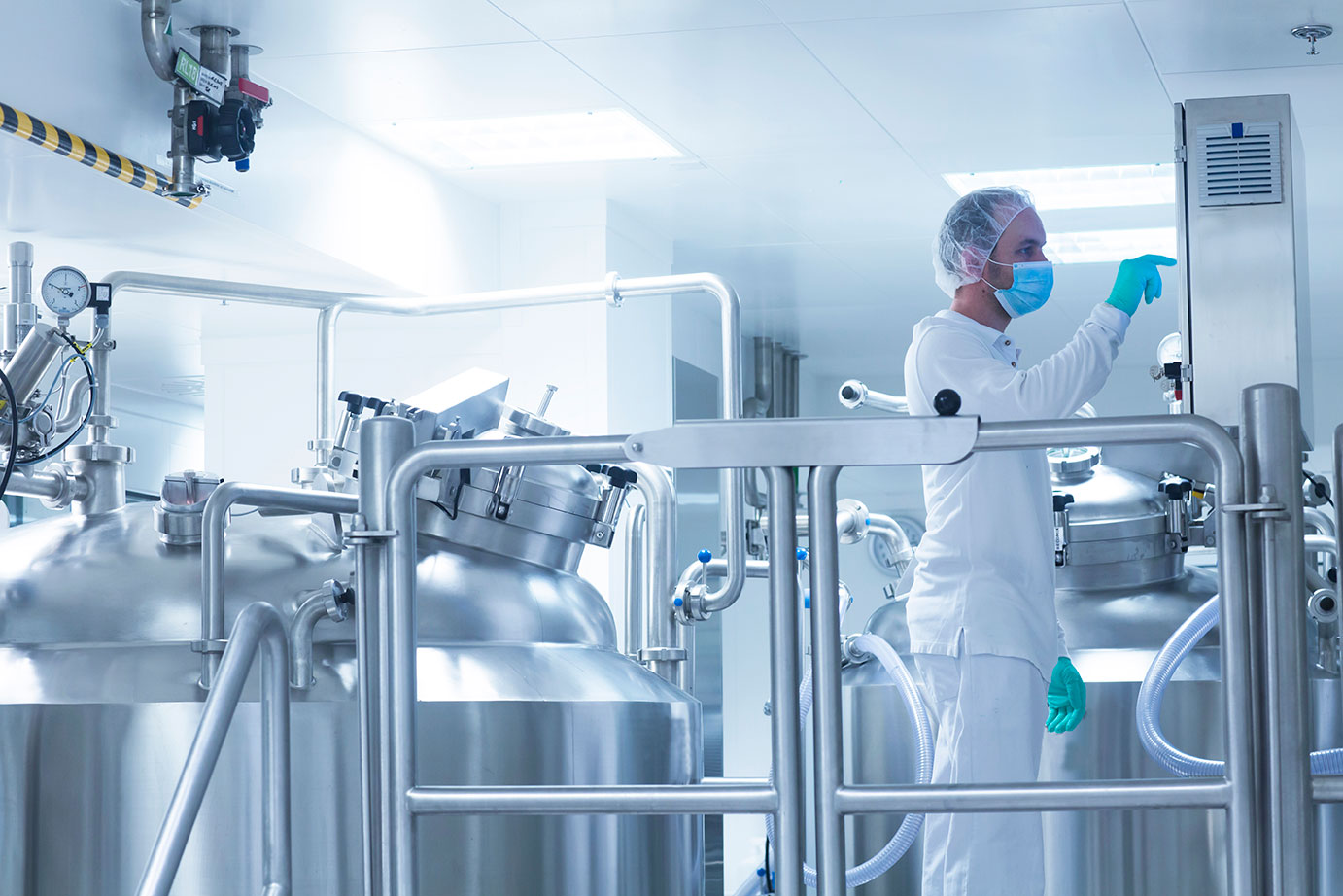
Biotech Boom: Britain's Bold Leap into Advanced Therapy Manufacturing
2025-02-19 21:00:56
Manufacturing
Blackstone Bullish: How Trump's Tariff Strategy Could Revive American Manufacturing
2025-03-12 12:13:49