Plasma Pen Breakthrough: How Tiny Tech is Transforming Industrial Bonding Forever
Manufacturing
2025-02-20 14:23:54Content
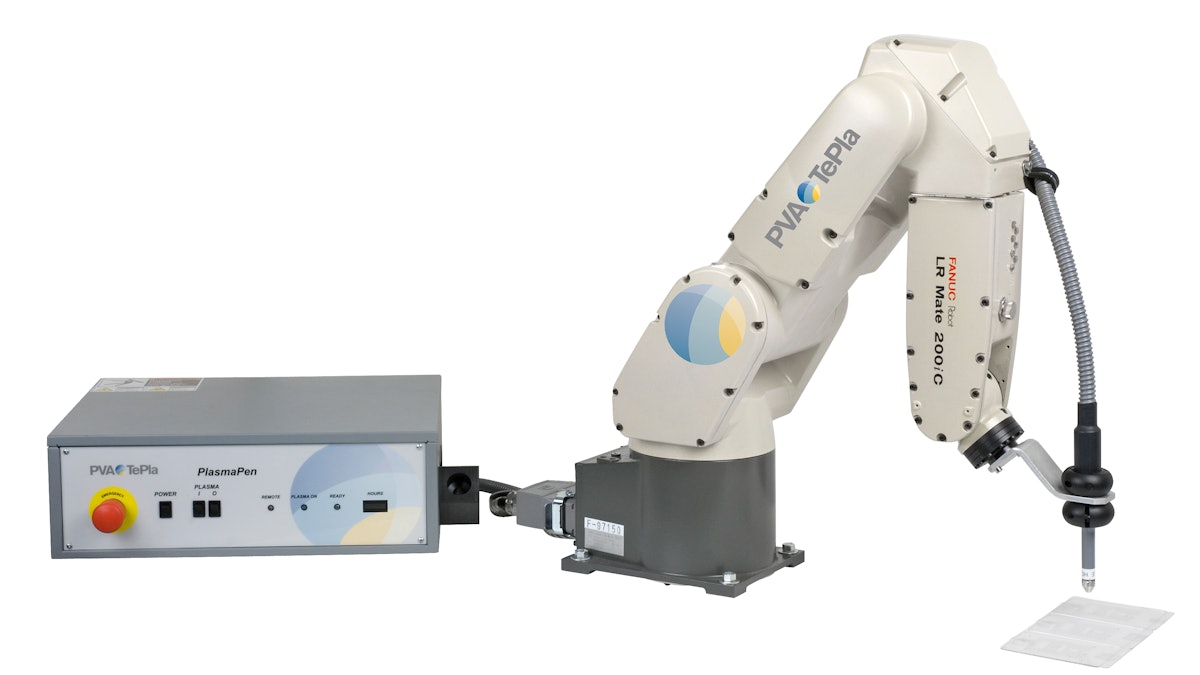
Revolutionary Plasma Technology Transforms Manufacturing Precision
In a groundbreaking advancement for industrial manufacturing, plasma "pens" are emerging as a game-changing solution for reducing equipment failure rates and enhancing production line reliability. These innovative tools leverage cutting-edge plasma technology to provide unprecedented surface treatment and quality control.
Manufacturers are discovering that integrating plasma pens directly into production lines can dramatically improve component performance and longevity. By creating microscopic surface modifications, these advanced devices help eliminate potential weak points and contamination that traditionally lead to equipment failures.
The technology works by generating a highly energetic plasma stream that can clean, activate, and modify surface properties of materials with remarkable precision. Unlike traditional treatment methods, plasma pens offer a non-contact, environmentally friendly approach that can be seamlessly incorporated into existing manufacturing workflows.
Early adopters in aerospace, automotive, and electronics industries have reported significant reductions in failure rates—some seeing improvements of up to 40% in component reliability. As manufacturers seek more efficient and cost-effective quality control methods, plasma pen technology represents a promising frontier in industrial innovation.
With continuous research and development, these plasma technologies are poised to revolutionize how industries approach surface preparation and equipment maintenance, offering a smarter, more precise path to manufacturing excellence.
Revolutionary Plasma Technology: Transforming Manufacturing Precision and Reliability
In the rapidly evolving landscape of advanced manufacturing, technological innovations continue to push the boundaries of precision, efficiency, and quality control. The emergence of cutting-edge plasma integration technologies represents a quantum leap forward, promising to revolutionize production processes across multiple industrial sectors.Precision Engineering Meets Breakthrough Innovation
The Rise of Plasma Pen Technologies in Modern Manufacturing
Advanced manufacturing environments are experiencing a transformative shift with the introduction of sophisticated plasma pen technologies. These innovative tools represent more than just incremental improvements; they signify a fundamental reimagining of surface treatment and preparation methodologies. By delivering highly concentrated plasma energy with unprecedented precision, these devices can fundamentally alter material characteristics at the microscopic level. Manufacturers are discovering that plasma pen technologies offer remarkable capabilities beyond traditional surface modification techniques. The concentrated plasma streams can instantaneously modify material properties, creating ultra-clean surfaces, enhancing adhesion characteristics, and dramatically reducing potential failure points in complex manufacturing processes.Technological Mechanisms and Performance Enhancement
The underlying scientific principles driving plasma pen technologies are rooted in sophisticated electromagnetic interactions. By generating highly energized plasma streams, these devices can effectively restructure molecular surfaces with extraordinary accuracy. The plasma stream acts as a dynamic cleaning and preparation mechanism, removing microscopic contaminants and creating optimal conditions for subsequent manufacturing steps. Engineers and researchers have extensively documented the remarkable performance improvements associated with plasma integration. Studies consistently demonstrate significant reductions in product failure rates, with some industrial applications reporting failure rate decreases of up to 40% when implementing advanced plasma treatment protocols.Cross-Industry Applications and Potential
While initially developed for specialized manufacturing contexts, plasma pen technologies are rapidly expanding across diverse industrial domains. Aerospace, electronics, medical device manufacturing, and semiconductor industries are particularly enthusiastic about these breakthrough technologies. The versatility of plasma treatment extends far beyond traditional surface preparation. Manufacturers are exploring innovative applications ranging from nanoscale material modification to complex coating processes. The ability to manipulate material properties at the molecular level opens unprecedented opportunities for product design and performance optimization.Economic and Operational Implications
The economic potential of plasma integration technologies cannot be overstated. By reducing failure rates, minimizing waste, and enhancing overall product quality, these technologies represent a significant value proposition for forward-thinking manufacturers. The initial investment in plasma pen systems is rapidly offset by substantial long-term efficiency gains and improved product reliability. Moreover, the environmental benefits are equally compelling. Plasma technologies typically require minimal consumable resources and generate negligible waste compared to traditional surface treatment methods. This alignment with sustainable manufacturing principles makes them increasingly attractive in an era of heightened environmental consciousness.Future Trajectory and Technological Evolution
As research continues and technological capabilities expand, plasma pen technologies are poised for exponential growth. Emerging developments in artificial intelligence and machine learning are expected to further refine plasma treatment protocols, enabling even more precise and adaptive manufacturing processes. Interdisciplinary collaboration between materials scientists, engineering experts, and manufacturing specialists will likely accelerate innovation in this domain. The convergence of advanced computational modeling, sophisticated sensor technologies, and plasma treatment methodologies promises to unlock unprecedented manufacturing capabilities.RELATED NEWS
Manufacturing

Robots, Algorithms, and Assembly Lines: How AI is Transforming Manufacturing's Future
2025-03-11 09:00:00
Manufacturing
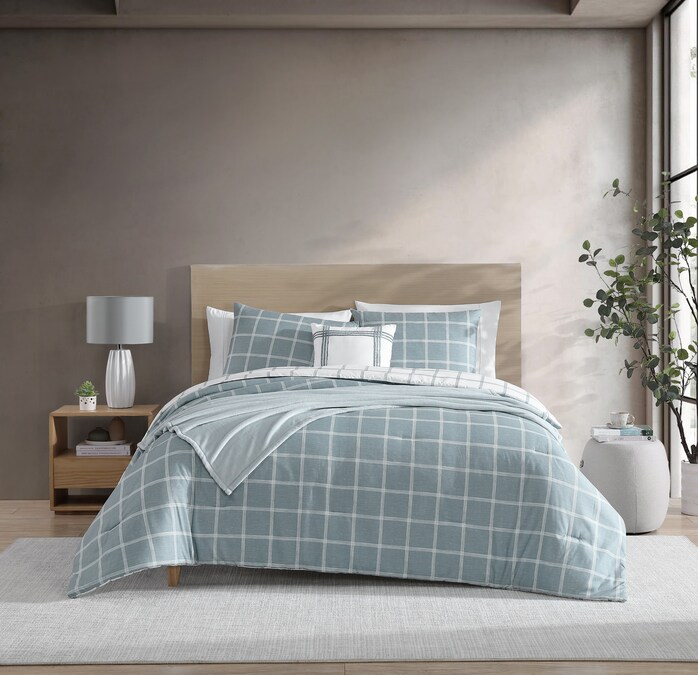
Home Decor Giant Cathay Inc. Supercharges Growth with Bold Expansion Strategy
2025-03-13 13:00:00
Manufacturing

Tech Giant Key Tronic Supercharges Springdale's Economy with Massive 400-Job Manufacturing Boom
2025-02-13 21:36:00